FEATURE ARTICLE, JUNE 2008
LOOMING PROBLEMS FACING CONSTRUCTION
Hint: Demand isn’t one of them. Richard Morris
Daily we listen to economists who warn that the United States is in the midst of a recession, and that it’s going to get worse before it gets better. There certainly is truth to this, but you’ll have to look outside of Houston — and most of Texas — to find visible evidence.
Our state’s diversified economy and geographic location seem to be giving it a degree of recession immunity, at least for now. The recent Forbes “Ten Fastest Growing U.S. Cities” list included three Texas cities, with Austin at No. 1, Dallas/Fort Worth coming in at No. 6 and Houston rounding out at No. 8. Job growth numbers released in April by the U.S. Bureau of Labor Statistics indicate Houston is growing at a rate of five times the national average and contributed 86,000 jobs in the 12 months ending February 2008. This accounts for one-tenth of the nation’s entire job growth, making Houston the best place in the country to look for a job. Combined with three other Texas cities, Texas is responsible for creating nearly a quarter of all new U.S. jobs last year.
The Lone Star State does not appear to be following the same economic model as the rest of the country, and this difference can bee seen in the extremely active construction market.
The five sectors required to feed a growing community — roadways, housing, utility/infrastructure, education and health care — are driven directly by the needs of a growing population and are validated by congested traffic, overwhelmed power grids, overcrowded schools and full beds in hospitals. This positive economic news is tempered by the energy crisis that affects us all and is in part causing the cost of construction materials to escalate. And, while construction growth is good, on the flip side is a labor shortage that makes it increasingly harder and more expensive to service the demand.
The Challenges
Material cost escalation is a major concern. The rising costs of oil and gas have increased transportation costs, causing the price of materials to rise at an accelerated pace. And the demand of the world market for construction commodities continues to strain an already challenged supply. Previously, pricing adjustments were normal every 6 months or so. Today, the cost of some materials increases within a single 24-hour period.
To outpace materials escalation, owners are expediting design and construction schedules so materials can be purchased sooner. As an example, while a design phase previously averaged 9 months and construction 30 months, today’s design may be condensed to 6 months with a goal of 24 months for construction. Additionally, projects are breaking ground sooner, and the design and construction phases are overlapping more, which may cause major issues with change orders throughout the construction process. (See The Shortening of the Timeline.)
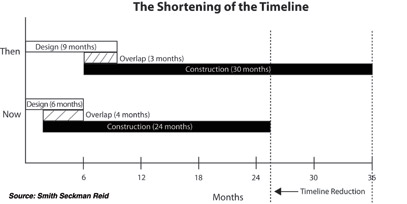
The labor shortage also is a huge problem. It’s true that Texas is likely the best place in America to look for a job, which is good news for workers. It’s also a challenging place to hire qualified workers, which is not such good news for those of us hiring.
Because of the recent slowdown in housing development, Houston’s 2008 labor market was predicted to remain flat. Anticipating that housing construction laborers would be available for commercial construction, developers in the Houston market did not expect a labor shortfall. However, the skill level of a residential laborer is less specialized than that of a commercial laborer, and a shortfall has in fact occurred.
As a result of the labor challenges, now when a project goes out for bid, there often are not enough bidders in the market to create healthy competition. Putting construction teams together is becoming increasingly challenging as well. In some cases, there are single or no bids at all, particularly on projects where prior owner/contractor/subcontractor relationships do not exist or are poor.
The Opportunities
To address the shortening design and building timeline, an integrated project delivery (IPD) method is being considered as a best practice. IPD utilizes the full potential of building information modeling (BIM) technology and lean construction practices to reduce the waste of time, materials and effort. BIM is an extremely valuable cost-saving tool where engineers and architects can generate a digital representation of the building design in the virtual world and detect system collisions and other problems before construction begins. Additionally in the IPD, the entire team of owner, designer and constructor are more entwined as stakeholders, resulting in stronger relationships and better project delivery.
Relationship building remains an extremely important tactic for addressing a challenging construction market. Subcontractors now have their pick of the litter when choosing their work. Understandably, they choose the people and companies that have treated them well in the past, and as a result, companies that have been less than fair with their subs are having the hardest time finding people to participate in their projects.
Similarly, out-of-town contractors without established relationships will not necessarily find Texas a market for easy work, at least not in the short term, unless they can bring their own labor. The tight labor pool is held by the known players, and an outsider with no reputation won’t fare much better than the local players with bad reputations. So, when selecting contractors, confirm the strength of their subcontractor relationships.
It’s good to be in a place where work is abundant. However, the challenges of material cost escalation and labor shortage will test the mettle of all of us in the industry who must continue to deliver despite these challenges.
Richard Morris is executive vice president of Smith Seckman Reid (SSR), an engineering design and facility consulting firm.
©2008 France Publications, Inc. Duplication
or reproduction of this article not permitted without authorization
from France Publications, Inc. For information on reprints of
this article contact Barbara
Sherer at (630) 554-6054.
|