COVER STORY, DECEMBER 2005
TRENDS IN CONSTRUCTION
Texas contractors reveal the latest methods and technology. Lindsey Walker
The construction industry is constantly evolving, and contractors must stay on top of the current trends in building methods and technology in order to be competitive. In light of the recent weather-related disasters along the Gulf Coast, as well as surging oil and energy prices, Texas' construction industry has been harder hit than some, causing the state's contractors to be even more aware of the changing marketplace. Though the extent of Hurricanes Katrina and Rita's impact on Texas' economy is yet to be seen, contractors are cautiously optimistic about what 2006 has in store for the Lone Star State.
“I think that construction in our area is going to be strong for the next 2 or 3 years,” says Phillip Bell, president of Arlington, Texas-based Bob Moore Construction. “Material prices are going to continue to rise with the economy and these natural disasters. It is going to become more of a problem to obtain good labor, and, because of that, labor-saving devices and labor-saving technology are going to become a lot more important and valuable — and people will be paying for it.”
Yet, with the cost fluctuations, some construction companies are having a hard time holding prices for developers and owners.
“Five years ago, or even more recently, you could put out a number and you knew that it was going to be a solid number for 6 months. Prices weren't changing very quickly,” says Neal Harper, president of Dallas-based Cadence McShane Corporation. “But now, with energy prices going sky high and petroleum-based products increasing in price by 30 percent to 50 percent during the last year or so, it's been hard in some areas to be able to hold prices. We've become more cautious in what we tell our owners.”
Saving Energy
In light of the energy and oil price increases, programs such as the Leadership in Energy and Environmental Design (LEED) implemented by the U.S. Green Building Council are becoming even more important for contractors and architects. Even cities are getting on board by giving permitting priority to new buildings that meet certain LEED levels. “The city of Santa Monica, California, for example, will cut your permitting time in half if you meet a certain LEED level with your new building,” says David Bloxom, president of Fort Worth, Texas-based Speed Fab-Crete. “I think Austin may be discussing doing that as well. This is going to be a big trend — to incorporate all these energy environmental issues into your new buildings.”
Harper agrees. “The environment is becoming a little more of a sticking point,” he says. “The LEED program, which deals with everything from using recycled material to taking care of the environmental aspects of the job, plays up to that fact.”
With the energy code that passed a few years ago, Harper notes that he's seen more energy-efficient mechanical requirements. “Some of the glass ratings are starting to become more important,” he says. “Now, you have to do an energy calculation that says ‘yes, we meet the energy code and here is how we meet it'. There are more requirements relevant to the energy efficiency of the glass, the mechanical aspects and the insulation — simply making sure the buildings are sealed tight and, from an energy standpoint, are really effective.”
Cadence McShane, for example, is currently planning a large residential project in Dallas called Park Place Apartments. The project, which will break ground in the spring, will be a high-rise building located off of Central Expressway and Park Lane. However, the energy code there dictates that the building can only be 40 percent glass. “Obviously, in high-rise residential, you want to have as much glass as possible to have the view over the downtown area,” Harper says. “We've been looking into some alternative materials there — higher glass product, better insulation and those sorts of things — to increase the efficiency of the energy requirements and allow us to go above that 40 percent.”
Technology Bytes
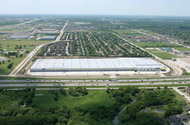 |
Bob Moore Construction employed Web-based technology when it built an 850,000-square-foot facility for Rooms To Go in Dallas (above). The client, which was in Atlanta, could watch the job site every day on the company's Web camera. “They could watch the concrete pours and all the activity on the site,” says Phillip Bell, president of Bob Moore Construction.
|
|
Energy efficiency concerns, however, aren't the only things that have changed in Texas' construction industry during the past few years. The marketplace is becoming more and more reliant on technology. Whether it is with electronic project management tools, web cameras or new construction equipment, the computer age has touched almost every corner of the general contracting field, making communication easier and business more efficient along the way.
“There is a whole host of new project management tools, as well as a lot of technology in the new construction equipment, such as cranes and backhoes,” Bloxom says. “There is computer-operated information on the equipment, and there is beginning to be construction technology around the whole issue of jobsite safety.”
“We do all of our bidding, project management, accounting and job costing on the computer,” Bell says. “We use the Internet as our platform so that, with a password, authorized people can access a set of plans or specifications or they can look at a drawing onscreen and make changes to it without anybody having to get on an airplane.”
Technological advances aren't just on the computer. New methods, such as Laser Screeds, allow companies to make large concrete slab floors with a high-degree of flatness as well as save time in labor. “It allows you to pour more concrete with a single pour with less man power,” Bell says. “At the same time, you get better quality out of it. That's one of the new things that has helped us out a lot.”
Clients are requesting these technological advances to be a part of their buildings as well. “Clients seem to be asking for a lot more high-tech electronic information systems,” Bell says.
“In terms of technology, clients are asking for things like wireless communication instead of hard-wired communication,” Harper says. “Those requests have become prevalent in the product types we're doing.”
Rebuilding the Future
Hurricanes Katrina and Rita and the growing energy costs will affect Texas' construction industry, but, it is yet to be seen exactly what the result will be.
“I think in Texas it will improve the construction economy,” Bloxom says. “Our company has already received calls from people wanting to use pre-cast concrete and other products that will hold up under hurricanes and not blow away like a lot of their construction did. The Texas market will continue to be good as long as we don't have super changes in our energy prices and excessive interest rate hikes.”
“We have seen labor resources leaving our market and going down to the Gulf Coast, and we have experienced significant price increases in building materials,” Bell says. “I think things will settle down in the next year and become more stable as building programs and plans get underway in New Orleans.”
Harper also is unsure of the impact. “I don't know that we really know the impact of the Gulf Coast issues,” he says. “We won't know what's going to happen until some of the reconstruction takes place. In general, however, the economic trends certainly have been upward.”
©2005 France Publications, Inc. Duplication
or reproduction of this article not permitted without authorization
from France Publications, Inc. For information on reprints of
this article contact Barbara
Sherer at (630) 554-6054.
|